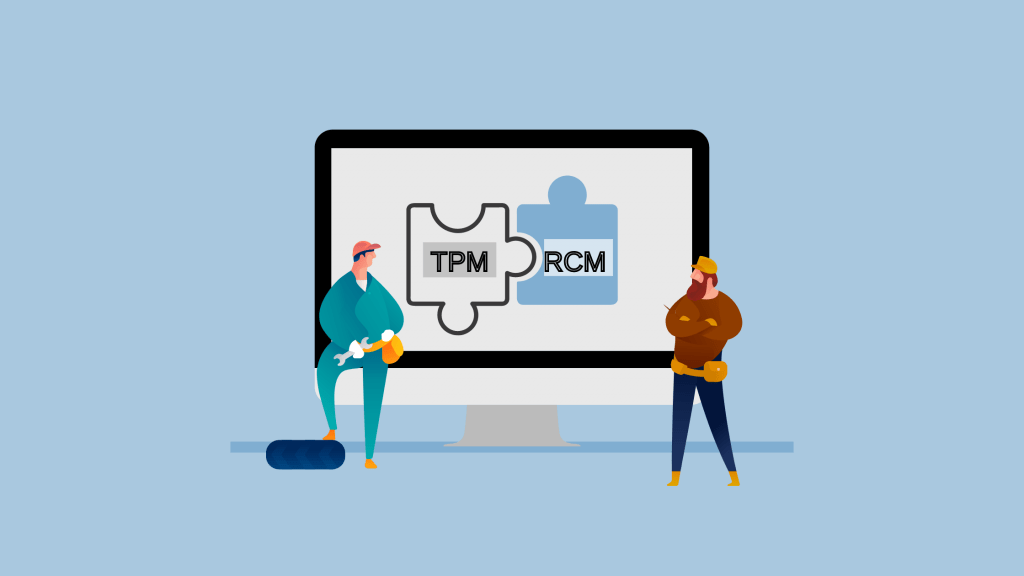
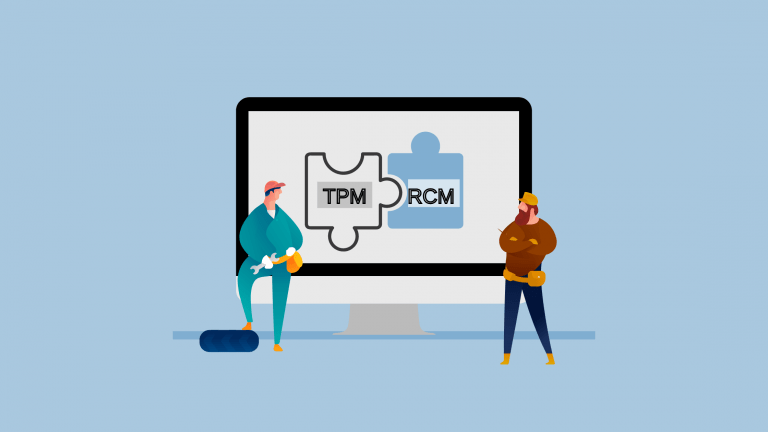
TPM y RCM: ¿Qué Significan en Mantenimiento?
Las estrategias de mantenimiento, desde la aparición de las máquinas y herramientas de trabajo mecánico, han ido progresando y continúan haciéndolo. Solo algunas se han establecido por su rendimiento y efectividad, dos de ellas son TPM y RCM.
En este artículo, exploraremos cada una para identificar sus diferencias y entender sus fundamentos. Te anticipamos que no son excluyentes, pero pueden ser más adecuadas para una u otra organización, así que toma nota y juzga por tu cuenta.
¿Qué es TPM y RCM?
TPM y RCM son dos de las estrategias más usadas para mejorar la gestión y el mantenimiento de activos.
A la hora de diseñar una estrategia de mantenimiento empresarial, los encargados encontrarán que existen muchas metodologías para hacerlo. Dentro de todas estas, existen dos que se han establecido en el tiempo por su efectividad:
- La metodología RCM (Reliability Centered Maintenance), o Mantenimiento Centrado en la Fiabilidad.
- La estrategia global TPM (Total Productive Maintenance), o Mantenimiento Productivo Total.
Si bien ambas estrategias no son excluyentes, trabajan en distintos niveles y lapsos. Como veremos a continuación, TPM incluye acciones que van más allá del mantenimiento.
Ambas prácticas significan una mejora en el uso de los activos de una empresa, pero al mismo tiempo sugieren protocolos distintos. Aun así, algo en lo que coinciden es en el uso de herramientas digitales, como los Software de Mantenimiento.
Fundamentos de TPM y RCM
Método RCM
Es una metodología para predecir fallas en equipos y componentes ––en un contexto específico y bajo ciertas condiciones de funcionamiento–– y ajustar las tareas de mantenimiento de forma proactiva.
Las características de RCM son:
- Trabaja solo en el área de mantenimiento.
- Tiene plena vigencia en plazos cortos.
- Depende de la identificación del tipo de mantenimiento que corresponde a cada activo.
El objetivo del RCM es preservar el funcionamiento de los sistemas que rigen a los activos. Esto exige un proceso sistemático para definir sus límites y funciones, y para analizar fallas y desgastes.
El proceso se usa para determinar lo que debe hacerse con tal de asegurar que un elemento físico continuará desempeñando las actividades que se esperan de él en su contexto.
Veamos un ejemplo:
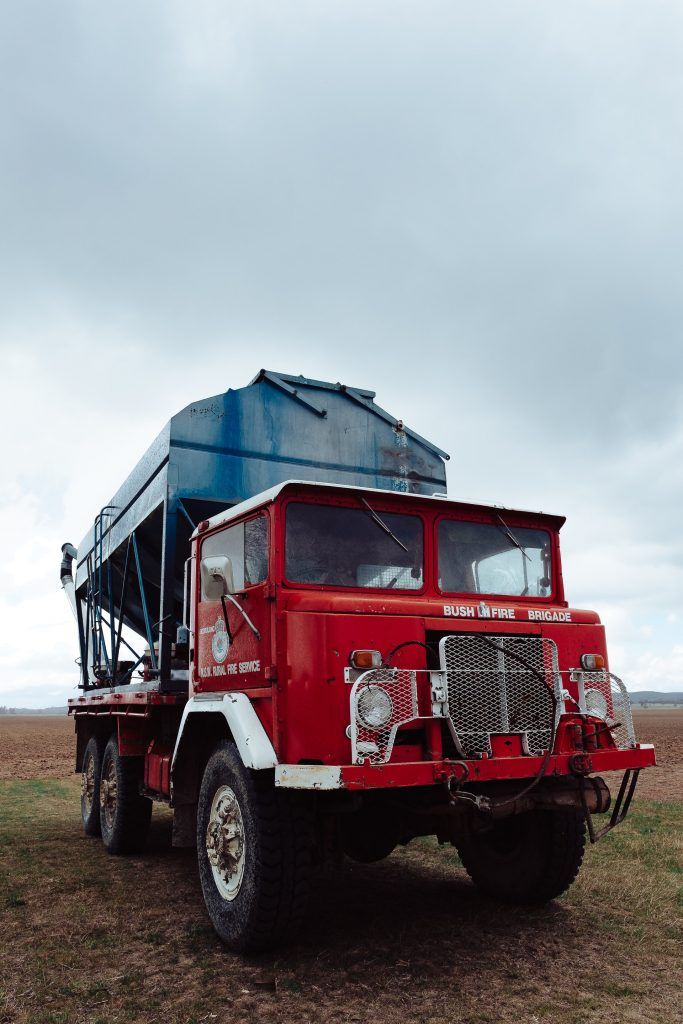
Hemos comprado una flota de camiones para nuestra empresa de logística, pero descubrimos que hacer el recambio de todos los componentes cada cierto tiempo no es rentable, ya que son muchas piezas las que, por sugerencia del fabricante, deben reemplazarse periódicamente.
Entonces, para descubrir cuáles son puntualmente los elementos críticos que se desgastan con el uso, sometemos un solo camión de la flota a una serie de pruebas emparentadas con el uso particular que vamos a darle a toda la flota (horas de manejo, distancia, condición de la ruta, etc).
Así, podemos determinar dónde y cómo vamos a realizar las tareas de mantenimiento sin caer en el reemplazo innecesario de componentes.
Las pruebas que sugiere RCM se basan en las siguientes preguntas:
- ¿Cuáles son las funciones que cumplen los elementos analizados?
- ¿Qué causa que fallen?
- ¿Cuáles son los efectos de su falla?
- ¿Qué se puede hacer para prevenir las fallas?
- ¿Qué sucede si no puede prevenirse la falla?
De esta forma, la técnica RCM nos permiten definir un tipo de mantenimiento particular, exclusivo para nuestros activos.
Método TPM
Acrónimo de Mantenimiento Productivo Total (Total Productive Maintenance). El modelo integra actividades de mejora continua y se caracteriza porque:
- Busca la eficacia económica a través de las metas: cero defectos, cero averías y cero accidentes.
- Se fundamenta en un plan de acción global que incluye a todo el personal de la empresa.
- Es una estrategia a largo plazo (necesita de 3 a 4 años para comenzar a dar frutos).
- Postula una nueva cultura organizacional basada en la participación de todos los trabajadores, la confianza y la cooperación.
TPM se basa en una filosofía integral, y en la idea de que ningún plan de mantenimiento puede ser efectivo si otros procesos generan pérdidas y fallas. Por ello, el objetivo es desarrollar habilidades competitivas en toda la organización, identificando y eliminando las deficiencias.
Estos procesos no se limitan a abordar los puntos débiles del equipo de mantenimiento, sino que se promueve la participación de todas las áreas y departamentos de la empresa.
Siguiendo nuestro ejemplo de la flota de camiones: por más específicos que sean los protocolos identificados para cada pieza, no servirá de nada si nuestros conductores no revisan los líquidos con regularidad, si cargan combustible de mala calidad o si eligen rutas en mal estado.
El TPM incluye la capacitación y entrenamiento del personal para lograr la implicación del operario como responsable de la calidad del producto que la empresa adquiere, y su fiabilidad operativa.
Esta práctica se considera una estrategia empresarial más que un modelo estándar de mantenimiento.
Diferencia entre TPM y RCM
La característica principal que debe considerarse para diferenciar TPM y RCM es su alcance.
- Si bien ambos buscan la mejor gestión de activos posible, TPM es una estrategia a largo plazo que apunta a mejorar el clima organizacional y el compromiso de los trabajadores.
- RCM, por otro lado, ignora las condiciones externas que inciden en el estado de los activos y se apoya en la condición básica del equipo, es decir, la idea de que el operario siempre tendrá un buen manejo y cuidado del activo.
- El método RCM da por descontado que el activo tendrá condiciones básicas de mantenimiento, y esto puede ser un error, sobre todo en un ambiente donde los operadores son causantes de la variación en la vida útil de los equipos.
- El RCM se promueve como una estrategia de mejora de mantenimiento, mientras que TPM reconoce que el mantenimiento por sí solo no puede mejorar la fiabilidad.
- TPM cree que todos los empleados deben involucrarse activamente en el mantenimiento de los activos. Cada miembro de la organización tiene que reconocer la necesidad de eliminar o reducir las pérdidas que afectan a la compañía, y enfocarse en la prevención de anomalías con el mismo ímpetu que los miembros del área de mantenimiento. Además, debe ser un compromiso de todos identificar y eliminar defectos.
Conclusiones
Las estrategias globales de mantenimiento, RCM y TPM, son normalmente utilizadas por grandes empresas, y su éxito dependerá de la disciplina y orden empresarial con que se ejecuten. Puedes revisar cuáles son las 6 principales pérdidas del TPM, en este enlace.
Contar con un Software de Mantenimiento será vital para ejecutar cualquiera de las prácticas comentadas en este artículo. Soluciones digitales como MP Versión 10 o Infor te permitirán gestionar los procesos de mantenimiento en tu negocio, asignar tareas, realizar monitoreos y diagnósticos de fallas.
Esto llevará a una buena de gestión de la información y del conocimiento para articular toda la información que un programa de mantenimiento, sea TPM o RCM, requiere.
1 Comments
Me interesa aprender más sobre el rcm y tpm, metodos de aplicación y gestión