
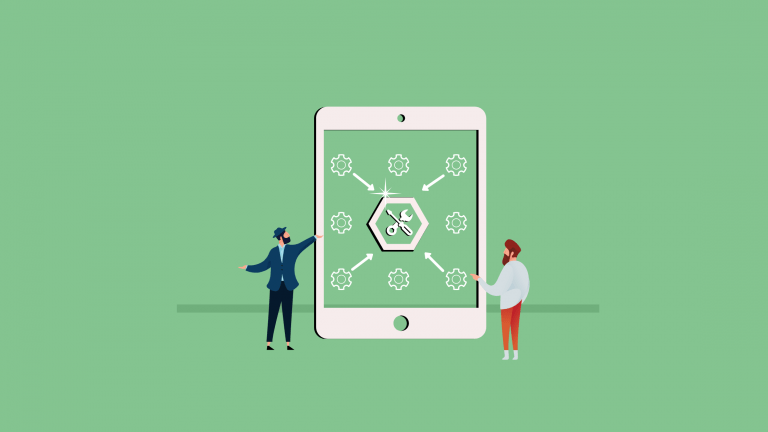
Mantenimiento RCM: ¿Qué es?
Con los años, han surgido muchas metodologías de mantenimiento para responder a las necesidades de las empresas. Una de ella es RCM (del inglés reliability-centered maintenance o mantenimiento centrado en la confiabilidad).
Hay mucha confusión alrededor del concepto RCM. Uno de los errores más comunes es confundirlo con el mantenimiento preventivo, puesto que ambos se enfocan en prevenir averías.
Para salir de dudas, en este artículo te explicamos qué es RCM exactamente y cómo se diferencia este método en la gestión de mantenimiento.
¿Qué es RCM en mantenimiento?
RCM son las siglas en inglés de reliability-centered maintenance o mantenimiento centrado en la confiabilidad (traducido también como fiabilidad a veces).
Esta tipología de mantenimiento surgió primero en la industria de la aviación para luego extenderse a otro tipo de organizaciones. La esencia del RCM es la identificación de problemas potenciales en componentes específicos para así tomar medidas antes de que la producción se vea afectada.
Una estrategia RCM incluso puede ayudar a una empresa a desarrollar nuevos métodos y programas especiales de mantenimiento para ciertos activos, dependiendo de las amenazas que se hayan identificado.
A veces, el RCM se confunde con el mantenimiento preventivo porque ambos apuntan a evitar fallas para que no tener que invertir tiempo ni dinero en mantenimiento correctivo. Sin embargo, la diferencia es que el RCM es específico, se concentra en activos o piezas determinadas, mientras que el mantenimiento preventivo es generalista.
Esta es una distinción importante, porque significa que el RCM en mantenimiento (si se administra bien) es mucho más eficiente que un plan de mantenimiento preventivo convencional.
Características de RCM
- La inspección de mantenimiento se enfoca en un activo o componente en específico. Por lo general, el departamento de mantenimiento se fijará en la maquinaria crítica para las operaciones de la empresa y en el costo de reparación vs. el costo de reemplazo. La decisión también tomará en cuenta lo que ha gastado la organización históricamente en mantenimientos previos, para así determinar el equipo que debe ser revisado.
- El RCM en mantenimiento involucra un análisis profundo de la situación para identificar las causas de un funcionamiento defectuoso. Ahora, hay muchas formas en las que una máquina puede fallar: rendimiento deficiente, velocidad de producción por debajo de lo normal, funciones incompletas o incluso puede pasar que el equipo esté haciendo algo para lo que no fue diseñado. Es importante determinar cuál está siendo el problema antes de poder hallar la solución.
- El RCM se destaca porque es una metodología flexible que se adapta a los objetivos y metas de la empresa. Por eso, propone abordar activos específicos en lugar de ejecutar un mantenimiento general donde no siempre es fácil detectar las causas de averías en el futuro.
Las 7 fases de RCM
El mantenimiento RCM se puede sintetizar en siete pasos que comprenden desde la selección del activo que la empresa necesita diagnosticar hasta la implementación de una nueva estrategia de mantenimiento, completamente personalizada.
1. Selección del activo
El primer paso es elegir un equipo para el mantenimiento RCM. Por norma general, la decisión debe basarse en la criticidad de los activos, es decir, cuáles son más importantes para garantizar la cadena productiva de la empresa.
Este tipo de máquinas deberían analizarse primero porque, en caso de fallar, su reparación o reemplazo sería mucho más costosa que la de un activo del que se puede prescindir.
2. Definición del alcance del análisis
El segundo paso es decidir qué tan profundo será el análisis RCM. Para esto, se deben conocer las funciones del equipo, qué espera la empresa de él, cuál debería ser su rendimiento ideal.
Con base en esto, el plan de diagnóstico buscará comprobar si la maquinaria está funcionando como debería o no.
3. Definición de los modos de falla
El tercer paso del proceso es determinar todos los posibles modos de falla del equipo a través de un Análisis de Modos de Falla (AMEF). Es decir, cómo y por qué la maquinaria podría comenzar a rendir menos de lo ideal: una velocidad de trabajo inferior, producción defectuosa, etc.
4. Identificación de las causas raíz para los modos de falla
Una vez identificados los modos de falla, el análisis dará un giro hacia las causas raíz de cada falla identificada. Por ejemplo, si una empacadora al vacío no está procesando el número de productos que se había planificado para una tasa de producción idónea, puede deberse a falta de lubricación o a problemas en el motor que impiden que el equipo trabaje como debería.
Ahora, si la empresa detectó más de una falla, entonces deberá indagarse en la causa raíz de cada una de ellas.
5. Evaluación de los efectos de la falla
Luego, es importante evaluar qué efectos puede tener cada falla en los equipos. ¿Hay afectaciones en el desempeño, en la seguridad o en el rendimiento de otras máquinas que hacen parte de la línea productiva?
Normalmente, cuando hay problemas técnicos en activos de alta criticidad, las consecuencias son graves en más de un aspecto. Puede que la rentabilidad de la empresa se vea afectada, pero también aumentará el riesgo de accidentes laborales.
6. Implementación de una táctica de mantenimiento para cada modo de falla
Según el diagnóstico realizado, los modos de falla vistos y las causas raíz identificadas, los especialistas de mantenimiento determinarán cuál es la mejor táctica específica para mantener en buen estado los activos.
La decisión estará basada en qué le conviene más a la empresa en términos económicos y técnicos, pero es muy frecuente que se elija como estrategia el mantenimiento CBM o basado en condición.
En caso de que los modos de falla detectados no puedan evitarse usando el mantenimiento CBM, lo más probable es que la empresa siga usando un modelo de mantenimiento preventivo, aunque rediseñado para atender mejor los requerimientos.
En ambas circunstancias, es indispensable que la organización incorpore un Software de Mantenimiento para monitorear el estado de los activos y el cumplimiento de los técnicos encargados.
7. Revisión periódica de la táctica de mantenimiento elegida
Por último, el mantenimiento RCM hace énfasis en darle seguimiento a la estrategia elegida en el paso anterior para comprobar que realmente funciona. Si llegan a descubrirse defectos, es importante presentar recomendaciones formales y continuar inspeccionando el nuevo plan de mantenimiento.
Una vez más, un Software de Mantenimiento es importante para darle seguimiento a los métodos de mantención de la empresa y poder medir su eficiencia. Esto puede hacerse definiendo indicadores de rendimiento o KPIs, que luego es posible registrar automáticamente usando un software profesional.
Conclusiones
- El mantenimiento RCM se caracteriza por enfocarse en activos específicos. De esta manera, se puede realizar un diagnóstico profundo para dar con todos los problemas que afectan el rendimiento de la maquinaria crítica.
- El objetivo del RCM en mantenimiento es rediseñar o crear nuevas estrategias de mantención conforme los modos de falla detectados y sus causas.
- El RCM es una de las metodologías de mantenimiento más flexibles que existen, ya que se puede adaptar a las necesidades específicas de una empresa y evitar que las ganancias se vean perjudicadas por averías.
Referencias:
«Reliability-Centered Maintenance: An In-Depth Look | Reliable Plant». 2020. Reliableplant.Com. https://www.reliableplant.com/reliability-centered-maintenance-31577.
«Reliability Centered Maintenance: What Is RCM? | Fiix». 2020. Fiix. https://www.fiixsoftware.com/maintenance-strategies/reliability-centered-maintenance/.