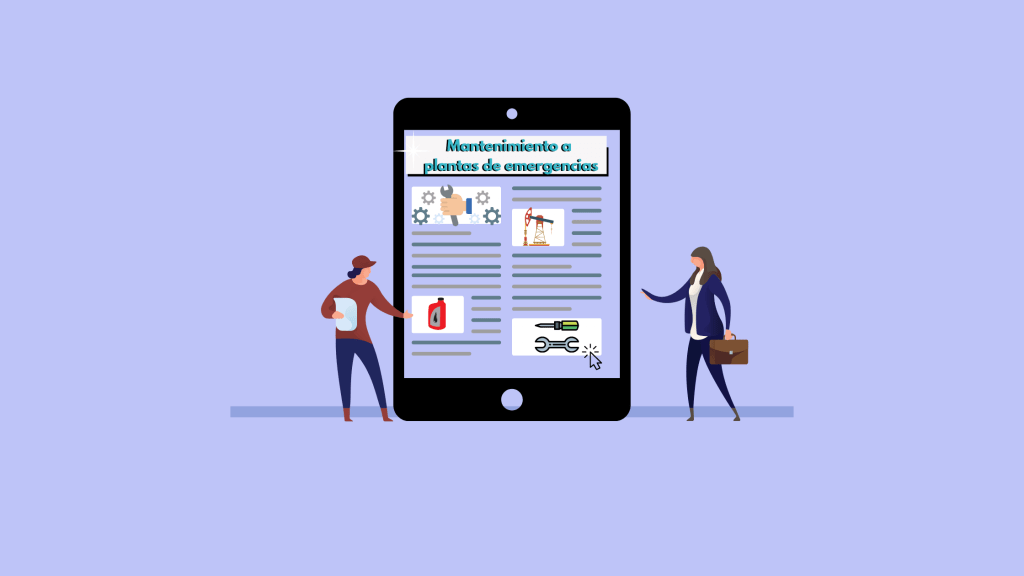
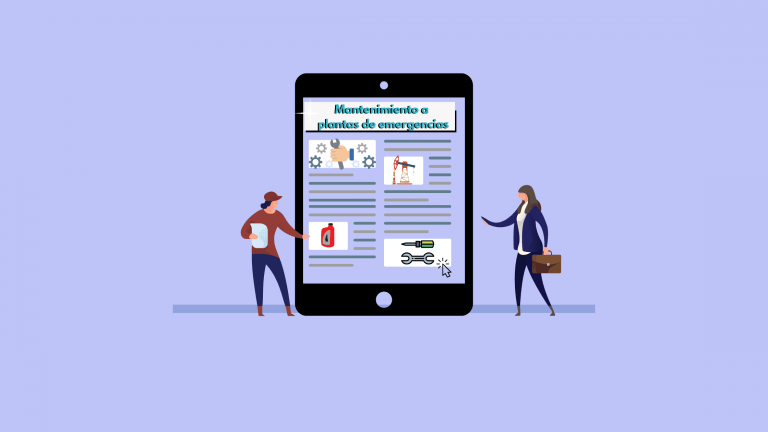
Mantenimiento a Plantas de Emergencia
Una planta de emergencia es una instalación que aloja equipos especiales para mantener el suministro eléctrico en caso de cortes de energía o apagones por fallas en el cableado externo.
Muchas organizaciones albergan pequeñas plantas de emergencia para garantizar que las instalaciones y máquinas sigan funcionando en situaciones extremas. Esto es muy normal, sobre todo, en:
- Hospitales y clínicas
- Aeropuertos
- Restaurantes
- Hoteles
Al igual que cualquier maquinaria industrial, los generadores de energía eléctrica necesitan mantenimiento para funcionar correctamente. Hoy veremos qué actividades incluye la gestión de una planta de emergencia.
Actividades de mantenimiento a plantas de emergencia
El mantenimiento en una planta de emergencia puede ser preventivo o correctivo. Las tareas correctivas dependerán del tipo de daño y muchas veces pueden ser no planificadas.
En cambio, el mantenimiento preventivo sí puede anticiparse y administrarse cuando hay una planeación adecuada (esto es, claridad en los cronogramas y modos de falla de los generadores).
Estas son las tareas más importantes de mantenimiento preventivo a plantas de emergencia.
Plantas de emergencia: mantenimiento preventivo
Sector | Actividades |
---|---|
Lubricación | 1. Revisión de aceite. 2. Búsqueda de contaminación o diluidos. 3. Detección de fugas. |
Combustible | 1. Inspección de combustible según consumo promedio, contaminación y densidad. 2. Diagnóstico de funcionamiento de bombas de transferencia. 3. Chequeo de seguridad. 4. Registro de la presión de combustible y la restricción de combustible de entrada. |
Aspiración | 1. Comprobación de tomas de aire y ductos. 2. Lubricación de actuadores de bypass y sistemas de compuerta de la caja de aire. 3. Revisión de seguridad de filtros de aire. 4. Registro de la presión del turbocargador. 5. Registro de la restricción de aire de admisión. 6. Examen de presión del cárter. 7. Chequeo de obturadores y limpieza de controles de cierre. |
Enfriamiento | 1. Inspección de niveles de refrigerante. 2. Prueba química anticorrosiva. 3. Prueba de presión. 4. Revisión de fugas. 5. Comprobación de aspas del ventilador y otras condiciones relacionadas con la seguridad. 6. Revisión del radiador. 7. Chequeo de bandas de polea del ventilador. 8. Revisión de rodamientos de polea. 9. Supervisión de mangueras y tubos de refrigerante. 10. Examen de temperatura del refrigerante. 11. Control de válvulas. |
Sistema de escape | 1. Revisión de tubos de escape. 2. Inspección de soportes del silenciador. 3. Diagnóstico del turbocargador. |
Controles | 1. Comprobación de controles de encendido, apagado y operación remota. 2. Calibración de instrumentos del generador y el motor. 3. Chequeo de indicadores, luces y alarmas. 4. Ajuste de potencia real y reactiva, frecuencia y voltaje. |
Generador eléctrico | 1. Registro de voltaje residual. 2. Verificación de ensamble del excitador, estator y campos. 3. Inspección de cableado y alambres. 4. Chequeo del rectificador rotativo y el supresor de onda. |
Estado mecánico | 1. Verificación de pernos de anclaje y tornillos. 2. Inspección de guardas del ventilador. 3. Comprobación de pantalla de toma de aire. 4. Búsqueda de rodamientos. 5. Supervisión de conexiones mecánicas. |
Sistema eléctrico del motor | 1. Inspección de cables de marcha del motor, conectores y alambres. 2. Registro de voltaje de flotación de baterías de arranque y nivel de electrolito. 3. Revisión del cargador de baterías. 4. Registro de corriente de funcionamiento de marcha. 5. Chequeo de controles eléctricos y sensores. 6. Comprobación de resistencia calefactora del agua, termostatos y contactor de desconexión de presión de aceite. 7. Prueba general de dispositivos de protección. |
Los peligros de una mala gestión de plantas de emergencia
Además del riesgo de no poder contar con suministro eléctrico en condiciones críticas, la mala gestión de plantas conlleva peligros para el personal, la obra civil y la comunidad en general.
En los peores casos, una planta de emergencia en mal estado puede causar:
- Incendios
- Explosiones
- Cortocircuitos
En los hospitales, es todavía más importante el mantenimiento de plantas de emergencia para evitar muertes por el cese del funcionamiento de aparatos médicos.
Ahora, la gestión del mantenimiento en una planta de emergencia involucra muchos procesos de planificación, ejecución y monitoreo. Por eso, las compañías y organizaciones aprovechan los Software de Mantenimiento para dar seguimiento al estado de la planta y verificar que los técnicos estén cumpliendo el programa.
Conclusiones
- Las plantas de emergencia son un recurso valioso en empresas de servicios como los hoteles y restaurantes, al igual que en los centros médicos.
- Para asegurar su buen funcionamiento, las plantas deben recibir mantenimiento periódico. El mantenimiento preventivo es una práctica importante para que la tasa de tareas reactivas se mantenga bajo control.
- Por otro lado, el mantenimiento a plantas de emergencia ayuda a disminuir el riesgo de accidentes como explosiones, incendios y cortocircuitos.
Referencias:
2020. Emergency power system basics: Maintaining always-on power for reliable healthcare. Eaton.Com. https://www.eaton.com/content/dam/eaton/markets/healthcare/knowledge-center/white-paper/emergency-power-system-basics-maintaining-always-on-power-for-reliable-healthcare.pdf.