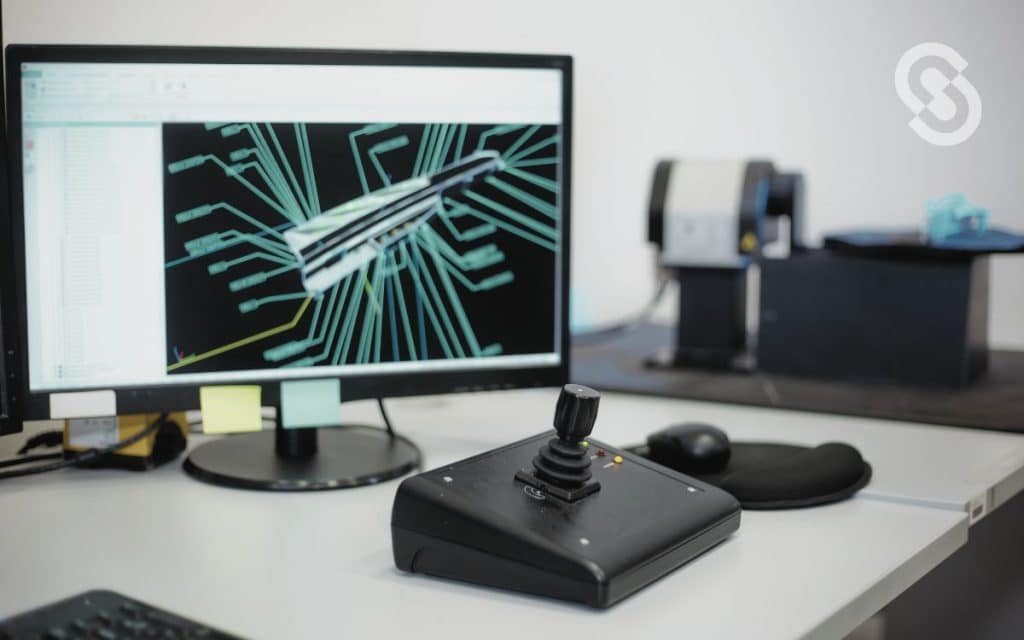
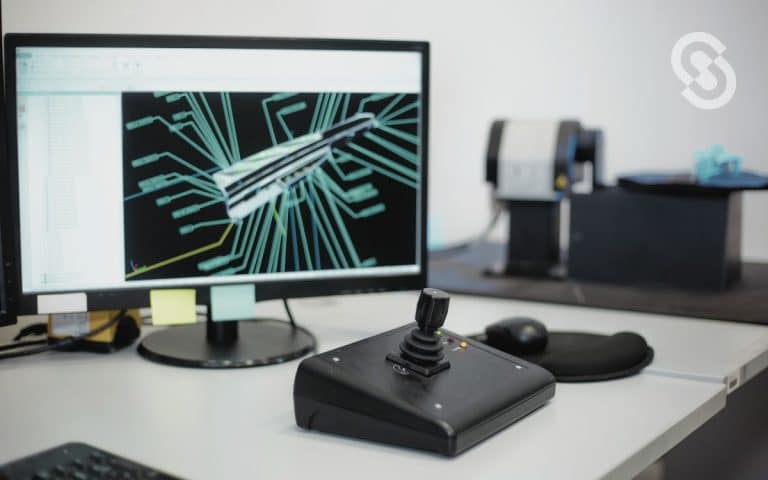
Simulación de procesos industriales: fiabilidad para tomar decisiones
La simulación de procesos industriales garantiza un camino seguro hacia la búsqueda de la optimización y mejora continua. Esta metodología, enraizada en la simulación de eventos discretos, se despliega como una herramienta computacional avanzada que permite analizar y prever con anticipación los posibles movimientos de un sistema.
Su principal cometido es la construcción de modelos dinámicos que representan fielmente fábricas o sistemas logísticos. De esta manera, plantea un horizonte donde la eficiencia y la precisión son primordiales.
En este artículo te guiaremos por los principales elementos que componen la simulación de ingeniería industrial, su importancia, beneficios y fases.
¿Qué es un simulador de procesos industriales?
Podemos definir la simulación de procesos industriales como el uso de modelos informáticos para evaluar y analizar los diferentes métodos y procedimientos de un sistema de fabricación.
El propósito entonces de estos modelos es prever el comportamiento de sistemas en diversas situaciones, permitiendo una exploración detallada de posibles cambios y sus repercusiones. Este ejercicio de anticipación es invaluable, ya que brinda la oportunidad de validar hipótesis y estrategias antes de su implementación efectiva en el terreno real.
En esencia, estas soluciones actúan como un laboratorio virtual, donde cada experimento, libre de riesgos físicos o financieros, allana el camino hacia la optimización y mejora continua.

Un ingeniero, por ejemplo, puede emplear la simulación de procesos para predecir cómo un ajuste en el caudal de un intercambiador de calor influirá en la cadena productiva. Este tipo de simulaciones, comúnmente basadas en software y accesibles a través de plataformas en la nube, proporcionan una interfaz intuitiva y visual, transformando datos complejos en información comprensible y manejable.
La capacidad de estudiar los cambios, prever sus consecuencias y adaptar estrategias en un entorno controlado y flexible, es lo que convierte a la simulación de procesos industriales en una herramienta indispensable para la industria moderna.
Más allá de la toma de decisiones y la planificación estratégica, la simulación se erige también como un recurso didáctico de primer orden. Los modelos de simulación, con su naturaleza interactiva y su capacidad para visualizar conceptos abstractos o complejos, se revelan como una vía excepcional para la formación y el desarrollo de habilidades en el ámbito de la ingeniería industrial.
¿Por qué es importante la simulación de procesos industriales?
El incremento constante en los costos de materiales, transporte y mano de obra, conduce a las empresas a buscar optimizar sus operaciones, minimizando gastos y maximizando rendimientos.
De esta manera, la simulación de procesos permite la evaluación exhaustiva y meticulosa de cada aspecto de la producción. Y al mismo tiempo, ofrece un entorno seguro y económico para experimentar con cambios, desde ajustes menores hasta transformaciones radicales.
Esta metodología se convierte en el escenario ideal para la aplicación de principios de eficiencia operativa como Lean Manufacturing y Six Sigma, permitiendo una comprensión profunda y una mejora continua de los procesos.
A diferencia de métodos tradicionales basados en hojas de cálculo, la simulación de procesos ofrece una vía rápida y efectiva para la modificación de parámetros y la obtención de resultados, garantizando decisiones informadas y respaldadas por datos.
Beneficios y desafíos de la simulación de procesos industriales
Las decisiones en el ámbito industrial a menudo implican significativas inversiones económicas y cambios sustanciales en el sistema productivo. Por lo tanto, la principal fortaleza de la simulación de procesos industriales radica en su confiabilidad para la toma de decisiones críticas.
Además, los beneficios de esta herramienta son múltiples y abarcan distintos aspectos:
- Optimización de Procesos: La simulación permite un análisis profundo de los procesos, facilitando la identificación de mejoras, diagnósticos precisos y la evaluación de distintas alternativas.
- Búsqueda del Proceso Óptimo: La herramienta es esencial para equilibrar líneas de producción, gestionar inventarios de manera eficiente, distribuir adecuadamente las cargas de trabajo y, crucialmente, identificar cuellos de botella.
- Planificación Basada en Modelos Predictivos: La simulación es un aliado en la planificación y pronóstico, ofreciendo modelos que reflejan con precisión el impacto de los cambios propuestos.
Sin embargo, es crucial reconocer que, a pesar de sus numerosas ventajas, la simulación de procesos industriales puede presentar desafíos. En primer lugar, los modelos de simulación requieren de inversiones tanto económicas como temporales. Si estas no se gestionan adecuadamente, pueden convertirse en gastos en lugar de inversiones fructíferas.
Además, la precisión de los modelos depende en gran medida de la calidad y relevancia de los datos ingresados. Por ello, es fundamental un enfoque bien definido y una implementación cuidadosa que garantice un reflejo fidedigno de la realidad y aporte valor real al proceso productivo.
Aplicaciones de la simulación de procesos industriales: Ejemplos
La simulación ingeniería industrial abraza un espectro amplio de aplicaciones. Desde la optimización de líneas de producción y montaje hasta la gestión refinada de inventarios y sistemas de transporte, los modelos de simulación se convierten en un aliado estratégico.
Aquí, se exploran algunas de las aplicaciones más destacadas:
1. Optimización de Máquinas en Operación
La simulación juega un papel crucial en el perfeccionamiento de la maquinaria industrial. Mediante modelos precisos, se pueden prever y mejorar aspectos como la eficiencia energética, la capacidad de procesamiento y el mantenimiento preventivo. Todos estos elementos aseguran que cada equipo funcione en su máximo potencial.
2. Revisión del Rendimiento de Complejos Industriales
A través de la simulación, es posible crear representaciones detalladas de complejos industriales enteros. De este modo, se contemplan no solo los eventos discretos, sino también variables críticas como cargas operativas, posibles fallos de equipo y variaciones en los procesos. Este enfoque integral promueve la creación de instalaciones más eficientes, seguras y resilientes.
3. Análisis de Confiabilidad y Productividad
La simulación ofrece un medio para identificar y evaluar puntos críticos y potenciales fallas en los sistemas de producción. Métodos como el Análisis RAM (Confiabilidad, Disponibilidad y Mantenibilidad) permiten diagnosticar y prever la disponibilidad y rendimiento de los procesos. Lo cual facilita la toma de decisiones proactivas y basadas en datos.
4. Optimización de la Capacidad de Producción
Mediante la simulación, las empresas pueden analizar y ajustar la capacidad productiva de sus sistemas. Aquí se pueden identificar anomalías o ineficiencias que podrían estar afectando la productividad. Esta herramienta es fundamental para garantizar que cada aspecto del proceso productivo esté alineado con los objetivos de eficiencia y calidad.
5. Mejora de Procesos Logísticos
La gestión logística, desde la adquisición de materiales hasta la entrega del producto final, puede beneficiarse enormemente de la simulación. Modelos detallados de la cadena de suministro permiten analizar y mejorar cada etapa. En consecuencia, se optimizan aspectos como el manejo de inventarios, la planificación de rutas y la coordinación con proveedores.
6. Monitoreo de la Sanidad y Seguridad
En un contexto donde las condiciones sanitarias y de seguridad son primordiales, la simulación emerge como una herramienta clave para prever y mejorar estas condiciones.
Los modelos de simulación permiten analizar y optimizar aspectos críticos como los protocolos de seguridad, las condiciones de trabajo y el cumplimiento de normativas sanitarias.
Fases de un proyecto de simulación de procesos industriales
El desarrollo de un proyecto de simulación de procesos industriales es un viaje estructurado que atraviesa diversas etapas, cada una con su relevancia y complejidad inherentes.
Esta metodología secuencial asegura que cada fase del proyecto se construya sobre una base sólida de conocimiento y análisis, maximizando las posibilidades de éxito y optimización del proceso industrial.
Veamos cuáles son las fases esenciales en este proceso:
1. Planteamiento de un Problema
Todo comienza con la identificación y comprensión profunda del problema. Es en esta etapa donde especialistas y stakeholders se sumergen en la situación, definiendo claramente los objetivos, los resultados esperados, el plan de prueba y las variables críticas.
Este diálogo inicial y constante con el cliente garantiza que la simulación esté perfectamente alineada con las necesidades y expectativas reales del proceso industrial.
2. Diseño de un Modelo Conceptual
Aquí se construye la estructura del proyecto. El modelo conceptual es una representación de los elementos del sistema y la interacción entre ellos.
De hecho, esta fase requiere un enfoque detallado en las relaciones lógicas y matemáticas, asegurando que el modelo refleje fielmente la realidad y las dinámicas del proceso industrial.
3. Colección de Datos
Los datos son el combustible que alimenta la simulación. En esta etapa, se realiza una recolección exhaustiva y un análisis meticuloso de los datos que serán la base del modelo. La calidad y precisión de los datos recogidos son fundamentales para la validez y confiabilidad del modelo de simulación.
4. Verificación y Validación
Esta fase es crucial para la credibilidad del modelo. Implica una serie de pruebas y evaluaciones para asegurar que el modelo conceptual funciona de acuerdo con la realidad.
La verificación se enfoca en comprobar que el modelo está construido correctamente, mientras que la validación asegura que el modelo es una representación precisa del sistema real.
5. Análisis de Resultados
Una vez que el modelo ha sido validado, se procede al análisis de los resultados. Esta etapa se centra en la interpretación de los datos obtenidos, la identificación de problemas o áreas de mejora. También podemos añadir la formulación de recomendaciones basadas en el conocimiento adquirido a través de la simulación.
6. Documentación
La transparencia y la comunicación son esenciales en cualquier proyecto de simulación. La documentación involucra la creación de un registro detallado de todo el proceso, incluyendo los métodos utilizados, los resultados obtenidos y las recomendaciones proporcionadas.
Para ello, herramientas y software de simulación modernos ofrecen interfaces intuitivas que facilitan este proceso, permitiendo una interacción fluida y la generación de informes comprensibles.
7. Implementación
La fase final y decisiva es la implementación de las soluciones derivadas del proyecto de simulación. Es el momento de llevar a la práctica las decisiones informadas y optimizaciones identificadas.
Durante esta etapa, es altamente recomendable contar con el apoyo continuo de los especialistas en simulación o del proveedor del modelo, para asegurar una transición fluida y efectiva de las recomendaciones a la realidad operativa.
Cada una de estas fases juega un papel vital en el éxito de un proyecto de simulación de procesos industriales, garantizando que cada decisión tomada esté respaldada por un análisis riguroso, datos precisos y una comprensión profunda del sistema en cuestión.
¿Por qué deberías usar un software para simular procesos industriales?
El uso de un software de simulación especializado es una necesidad imperante. Estas herramientas digitales avanzadas son el nexo entre las teorías complejas y su aplicación práctica y tangible.
Los sistemas industriales son conjuntos intrincados de variables y ecuaciones. Por lo que abordarlos de manera efectiva requiere una solución que no solo comprenda, sino que también pueda manejar y manipular esta complejidad con precisión.
Las funciones generales de un software de simulación abarcan diversas capacidades, cada una aportando valor significativo al proceso de simulación:
- Crear Informes y Analíticas: Permite analizar datos de pruebas y generar informes detallados para una comprensión profunda de los resultados.
- Realizar Modelados Matemáticos: Los software de simulación ofrecen herramientas para diseñar y ejecutar flujos de trabajo, asegurando precisión y relevancia en los modelos creados.
- Permitir la Manipulación Directa: La interactividad es un aspecto clave de los software de simulación modernos. Permiten a los usuarios interactuar directamente con el modelo, realizando acciones que son físicas, reversibles y progresivas, lo que enriquece la experiencia y ofrece una visión más intuitiva del sistema.
- Modelar en Tres Dimensiones: Su capacidad de diseñar representaciones tridimensionales de objetos y sistemas, ofrece una perspectiva más rica y detallada del proceso o producto en cuestión.
Conclusión
En definitiva, la simulación de procesos industriales representa un enfoque que anticipa la realidad y permite moldearla, mejorando los procesos industriales de manera significativa y sentando las bases para un futuro más eficiente y sostenible.
Esta herramienta es indispensable en la industria moderna, con la optimización y mejora de los sistemas productivos. Como así también una base sólida y confiable para la toma de decisiones informadas y la planificación estratégica.
1 Comments
Somos una empresa fabricante de juegos infantiles y mobiliario para exteriores con madera plástica reciclada.
Deseamos eficientar los procesos productivos para mejorar el servicio al cliente y la rentabilidad.
Requiero entender como un proceso de simulación virtual puede ayudarnos a lograr ese objetivo.